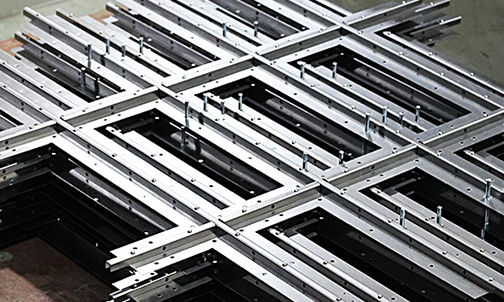
Online Custom Sheet Metal Fabrication Service
Sheet metal components and assemblies in as fast as 1 day. Get an online quote for your prototype or low-volume production project today.
Certifications
ISO 9001:2015 | ITAR Registered
Sheet Metal Fabrication Capabilities
Our online sheet metal fabrication service enables you get a quote in minutes and have your parts delivered in days. We offer 3D visualized Design for Manufacturability (DFM) feedback to help you manage project costs and receive actionable design insights. With a broad range of fabrication and finishing capabilities, our powerful combination of technology and skilled operators produce precision quality parts whether your project has one component or many.
Laser Cutting
Laser cutting is a subtractive manufacturing process that uses a high-powered and focused laser beam to create precise cuts in sheet metal materials.
Forming and Bending
Press brake forming uses a matching punch and die set and the application of force along a straight axis, producing linear bends on metal sheets.
Punching
Punching is a process that combines a punch tool with a bottom die and uses a pressing force to cut part profiles and form metal sheets into specific shapes and patterns.
Fabricated Assemblies
Sheet metal assemblies involve joining multiple sheet metal components through a variety of processes, such as welding or riveting, to create an assembled final product.
Sheet Metal Capability to Lead Time Map
Our online sheet metal fabrication service delivers components and assemblies to you in days. We offer a broad range of in-house fabrication and finishing capabilities to produce precision quality functional or end-use parts.
Fabrication Capabilities | Eligibility | Applications |
---|---|---|
|
Material thicknesses: ≤0.125 in. (≤3.175mm) |
|
Fabrication Capabilities | Eligibility | Applications |
---|---|---|
|
All material thicknesses: 0.024 in. - 0.250 in. (0.61mm-6.35mm) |
|
Fabrication Capabilities | Finishing Options | Applications |
---|---|---|
|
|
|
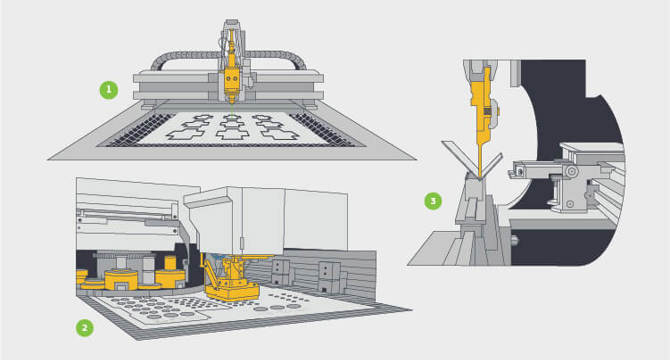
How Does Sheet Metal Fabrication Work?
During the sheet metal fabrication process, thin sheet metal stock is placed on a flat bed where a laser cutter (1) draws programmed part patterns. Depending on the part geometry, a sheet metal punch (2) can form additional features. Once the parts are deburred, they move to the press brake (3) where they are formed into the final geometries. Additional secondary operations are often used to finish the sheet metal parts.
Advantages of Sheet Metal Fabrication
The sheet metal fabrication process is ideal for metal components and can support both prototyping and production quantities.
- Low material waste
- Can cost-effectively scale to production volumes
- Multiple finishing options like anodizing and powder coating
Our Sheet Metal Fabrication Process
Unlike traditional sheet metal shops, we have infinite capacity and an easy-to-use online quoting system ensuring on-time shipment every time—whether you need a single part or 500 parts. You also have access to our team of knowledgeable engineers to optimize part designs and user-friendly online resources. Trim your production time and launch products faster with one local sheet metal supplier from prototypes to assemblies to finishing options.
View Design Guidelines |
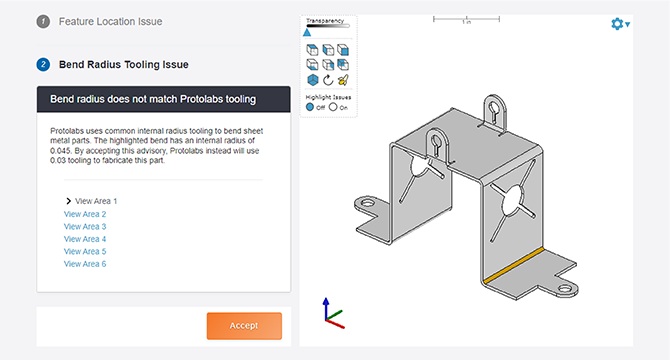
Design for Manufacturability (DFM) Feedback on Every Sheet Metal Quote
We now offer automated design analysis for all sheet metal components, which highlights any features that may pose challenges during the fabrication process. DFM feedback that can improve the quality of your sheet metal parts is now delivered in minutes.
Start a Project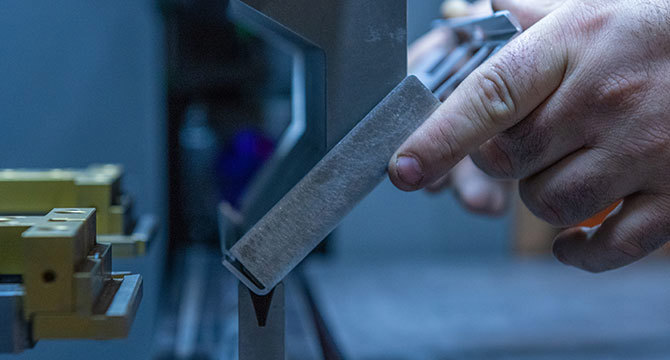
Sheet Metal Applications
Sheet metal is a versatile manufacturing process for a range of metal components. The process can support high-volume commodity products and low-volume, one-of-a-kind applications. Common sheet metal parts include:
- Electrical enclosure
- Parts for computer electronics
- Chassis
- Brackets
- Cabinets
- Mounts
- Appliances
Our Sheet Metal Material Options
- Aluminum(1)
- Brass (2)
- Copper (3)
- Stainless Steel(4)
- Steel: CR Non-treated (5)
- Steel: CR Galvanneal and CR Galvanized (6)
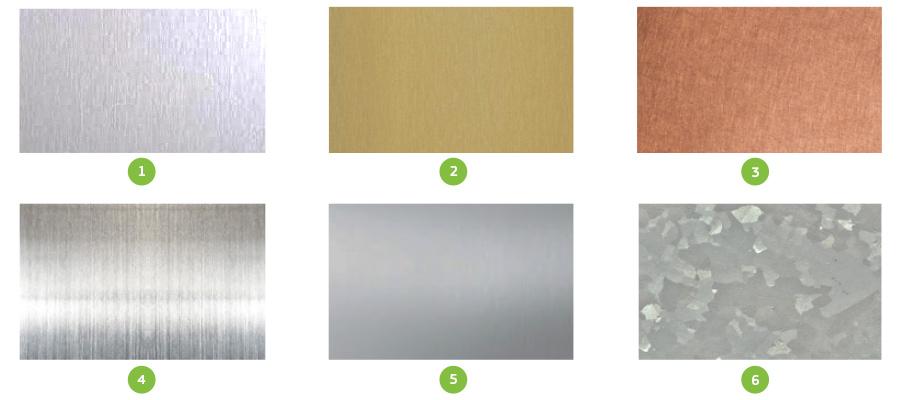
Why Choose HAPWAY for Sheet Metal Parts?
Fast and Simple Online Quoting
Our easy-to-use interface offers an average one-day upload-to-quote lead time (simple design quoting in as fast as one hour). Easily configure part specifications like material selection, and finishing options.
Reliable Delivery
Quality parts delivered within our five-day standard lead time.
Expansive Capacity
With more than 200 machines all under one roof, we’re dedicated to continuously evolving our capabilities.
Domestic Production
All sheet metal parts are made in New Hampshire with secondary operations such as hardware placement, welding, and finishing done in-house or locally by an approved vendor.
Sheet Metal Technical Expertise
Work with our team of engineering experts that offer technical design guidance and can inform you on manufacturability and cost-saving opportunities.
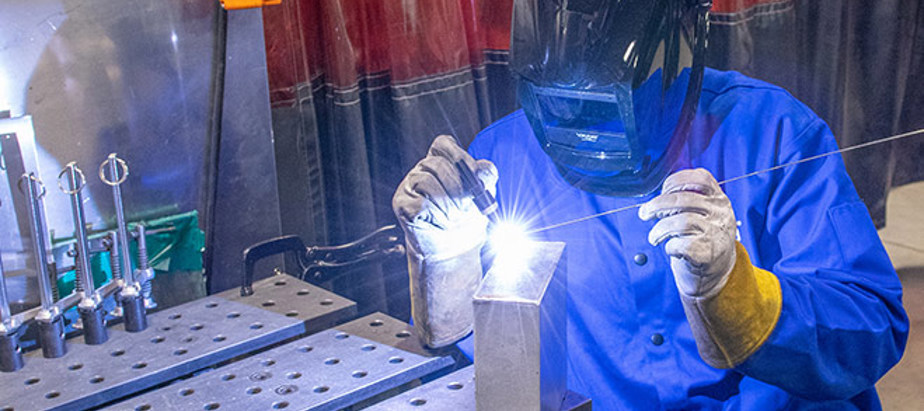
Sheet Metal Finishing Options
Looking for more than a few basic sheet metal parts? We offer welding, hardware insertion, plating, silk screening, and powder coating to provide complete sheet metal components all under one roof.
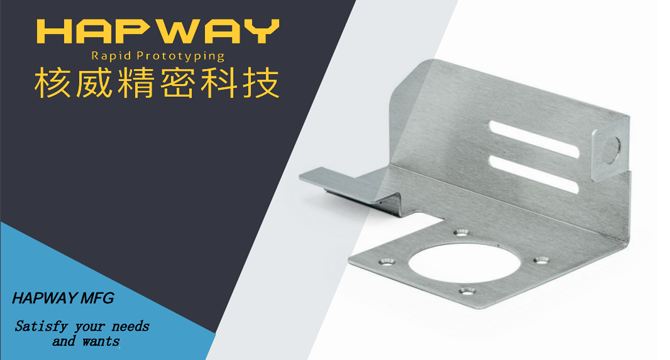
Sheet Metal Surface Finish Guide
Check out our sheet metal guide for a quick snapshot of our Standard and Cosmetic finishing options available for various sheet metal materials.
Download Guide